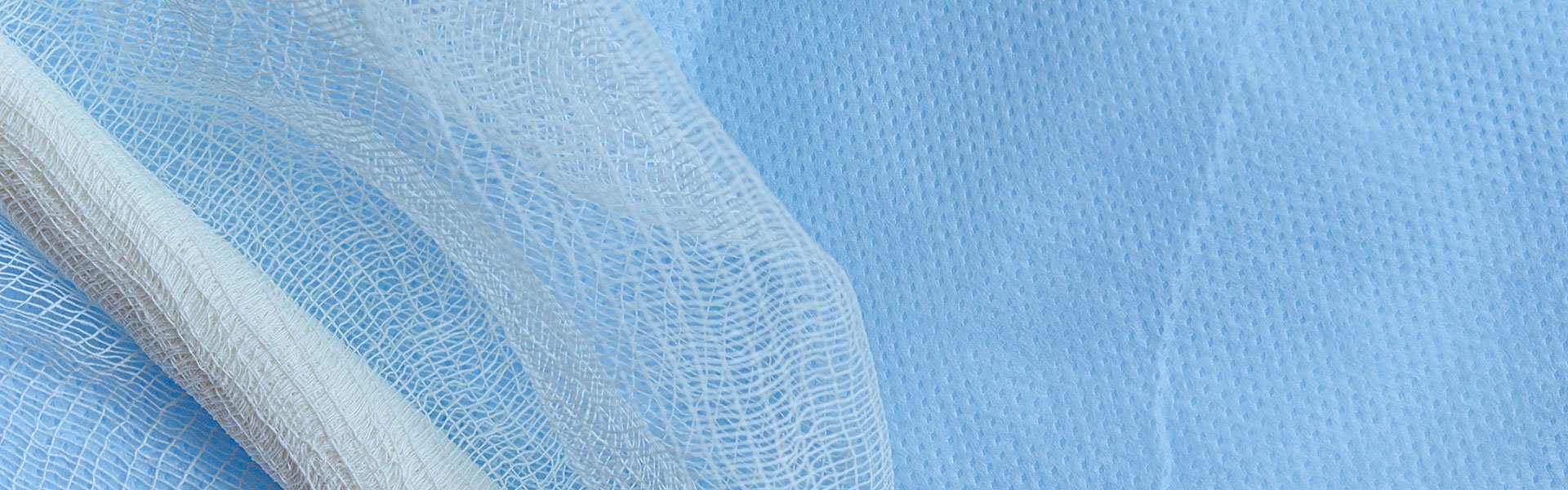
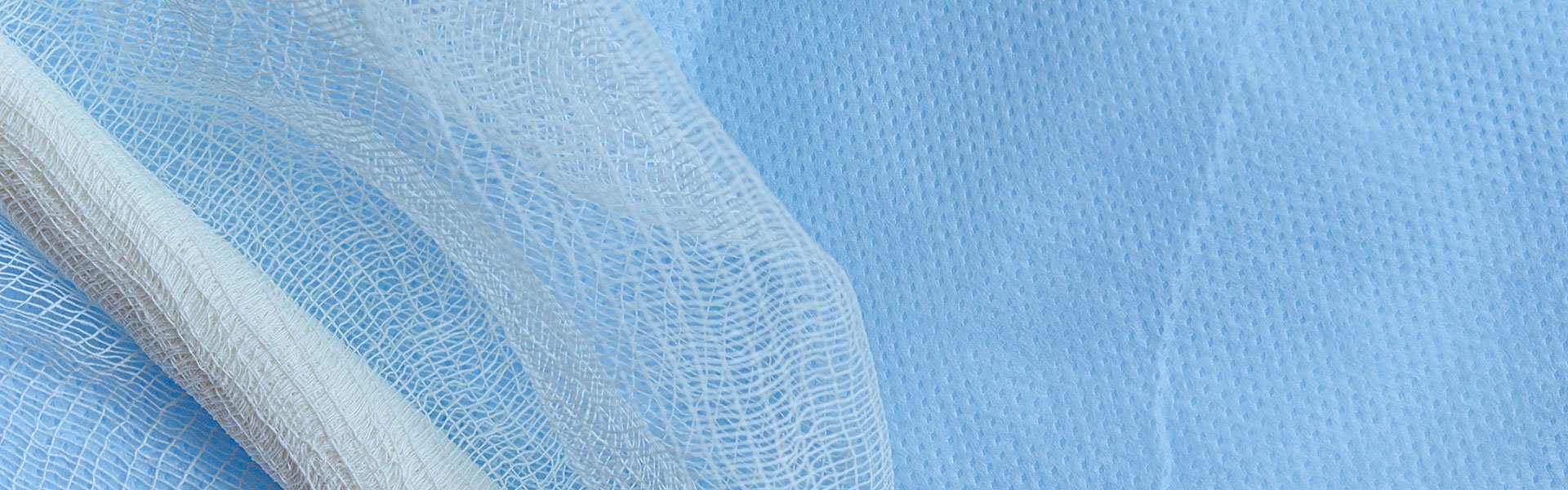
- Home
- Applications
Nonwovens
Nonwovens
Nonwovens production is a broad category of processes that convert fibres into mats, sheets or other final shapes for use in products.
Luwa solutions for these applications include air conditioning to control humidity for optimal fibre processing and pneumatically conveying fibres.
Key Factors in Web Forming / Bonding & Converting Process
Maintaining the correct humidity level is essential for smooth machine operation. Moisture reduces electrostatic charges, especially on synthetic fibres. But higher humidity increases lapping and reduces the effectiveness of disentangling and alignment. Also, breaking forces and elongation are directly influenced by the ambient humidity in the department. Optimum values vary depending on the use of the raw material and its mixture. A higher relative humidity will result in a lower room temperature during the evaporative cooling mode.
Not all industrial processes are equally sensitive to temperature fluctuations. For example, quenching air processes are highly sensitive and must be controlled within a narrow range.
However, all processes prefer a constant temperature, as most nonwoven raw material are hydrophilic and the moisture absorption capacity changes with temperature. In addition to reducing quality variation, temperature control has a positive effect on:
- reduced fibre fly in the process,
- fewer electronic failures of the machine control system and
- a better working environment for the employees.
Daily room temperature fluctuations can be minimized by using refrigerant cooling instead of evaporative cooling, especially during the summer months and monsoon rains.
Fibre Fly / Dust Contamination - In order to prevent unwanted infiltration of dust from the outside, the process is kept at constant overpressure. Depending on the outside air contamination, fresh air filters and, depending on the process requirements, supply air filters are required. Local regulations may set Permissible Exposure Limits (PEL) to protect nonwoven workers from byssinosis. Sufficient air changes throughout the process are required to dilute the dust levels and keep the departments clean and free of fly liberated from the machines.
Fibre Recovery and Disposal - Most Nonwoven Process machines have integrated suction points that can be incorporated into a fibre deposit system. The fibre separation and dust filtration plant must be designed in such a way that it can handle the required air volume and also the amount of waste fibre.
Depending on the raw fibres used in the plant, several fibre separators can be installed to separate the different materials from each other. Modern Fibre Depositing Plants are integrated with the Bailing Press systems and Briquetter to efficiently handle the dust collected at different sources of the Nonwoven Process and Converting lines.
The dependency on the fibre depositing system is essential for the operation of the process. A standstill of either the fibre depositing plant or the bailing system leads to an immediate shutdown of the entire process machine.
Web Forming and Bonding
Nonwovens manufacturing starts by the arrangement of fibres in a sheet or web.
Web Forming
These fibres can be staple fibres or filaments extruded from molten polymer granules.
- Dry Laid Carding
- Short Fibre Air Laid
- Wet Laid
- Spun Laid
- Melt Blown
- Submicron Spinning
Web Bonding
Webs have a limited initial strength right after the web formation, depending on various bonding mechanisms. Therefore, the web needs to be consolidated in one way or another. The choice of the web consolidation method strongly depends on functional properties that are needed, as well as on the type of fibres used.
There are three basic types of Bonding:
- Thermal Bonding
- Mechanical Bonding
- Chemical Bonding
Converting: Soft Disposables
Our proven system has decades of experience providing reliable temperature, humidity, and dust control.
Luwa provides a unique approach to the filtration and air conditioning solution for disposable diaper and feminine hygiene product manufacturing. The applications require the ability to capture both dust and fibers and the unique properties of Super Absorbent Polymer (SAP) used in these products require special care. The Luwa system provides better dust removal technique using a high efficiency filter that requires 1/3 the floor space of conventional rotary drum filters. And it can be combined with integral air conditioning components for the most economical upfront and operating cost.
Suction is provided to the production line machinery at the required points. Smooth metal duct conveys the dust and fiber laden air to the Luwa unit. Fiber is filtered out first by a rotary prefilter screen followed by the unique Rotary Pleated Belt filter. The air is either cooled with water coils or humidified with TexFogfogging sprays. Finally, it is supplied back to the manufacturing hall with a combination of metal and fabric ducts. Waste material is collected through the stripper vacuum system, including smooth metal duct, small high pressure fans, and a cylindrical pulse jet final filter. Waste fiber can be baled or reclaimed to the process and waste can be briquetted.
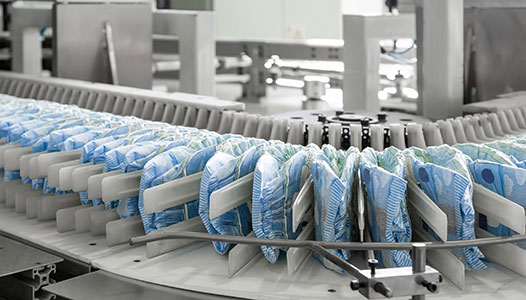
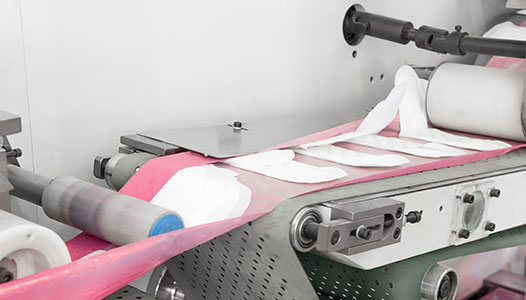
Features and Benefits
- High efficiency Pleated Belt Filter collects SAP at high efficiency and eliminates the need for multiple stages of static filters downstream, hence saving space
- Reduces operating system pressure drop and therefore energy consumed
- Reduces maintenance cost for replacement of the static filters
- Reduces landfill waste volume. Air exiting the filter is cleaned and sent directly to an A/C coil and humidification section
- Integration with air conditioning modules simplifies ducting reducing up front capital expense and operating energy cost
- Allows individual production lines to operate completely independently if desired for increased overall plant reliability
- Air conditioning module is completely hygienic using Reverse Osmosis (RO) filtered water in fogging spray for humidification – no stagnant or recycled water for hygiene application