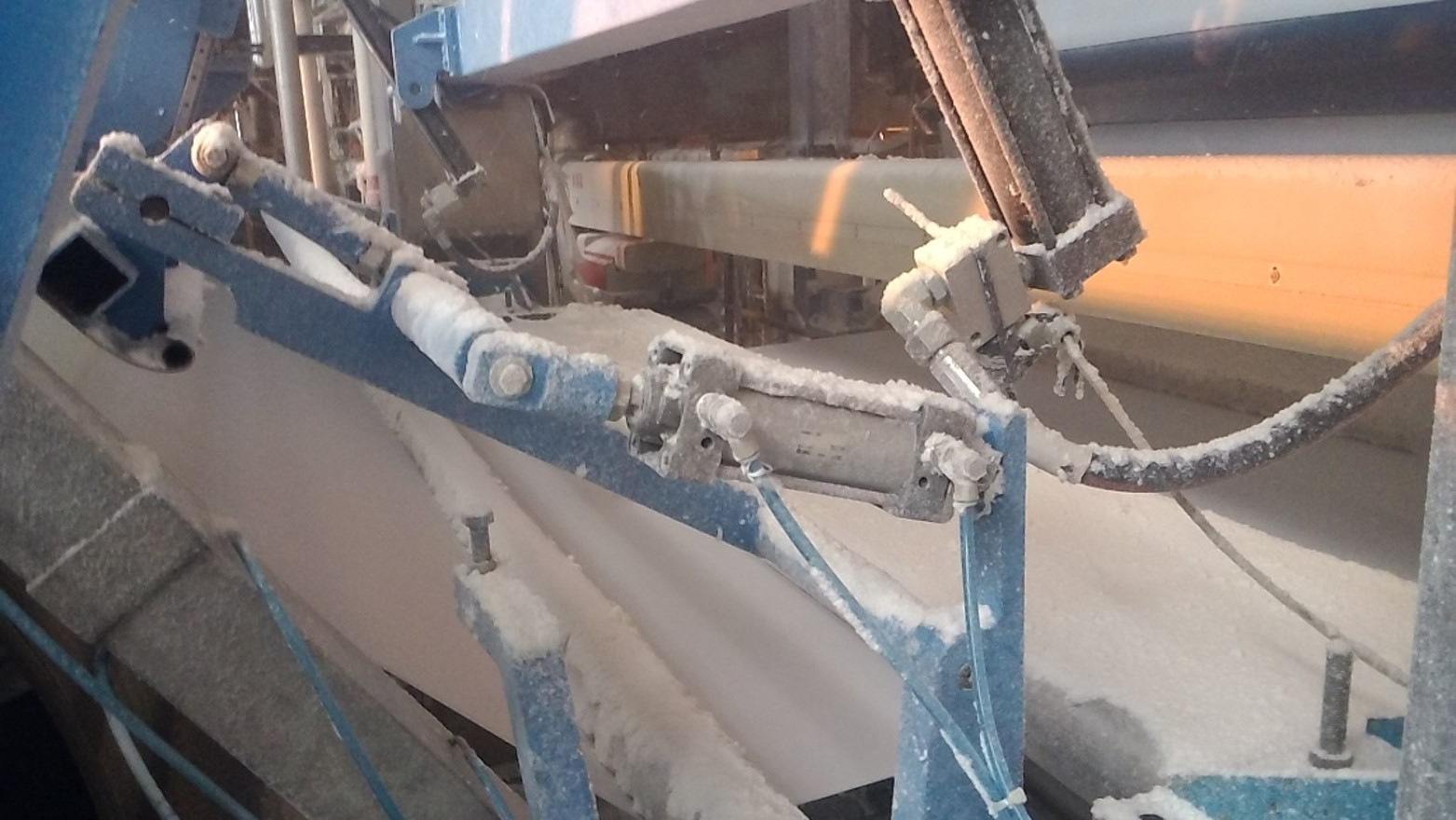
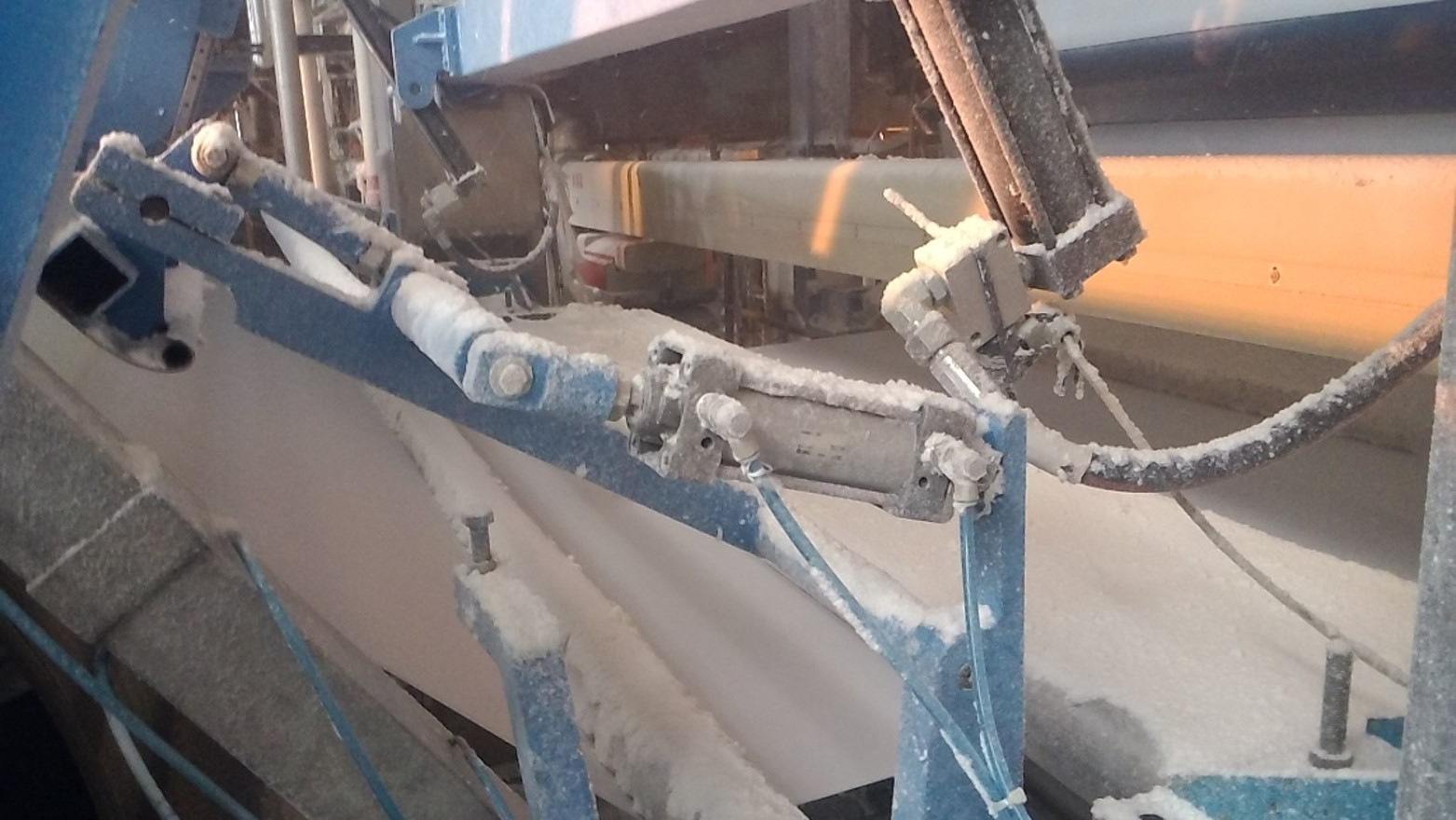
- Home
- Applications
Tissue Paper Dust Control
Tissue Paper Dust Control
Airborne dust from tissue paper can pose as a fire and health risk. Don't let dust stop your manufacturing. You can improve the environment of your workplace for your employees with Luwa's Complete Dust Handling Solution.
Tissue paper is thin, soft paper, produced on a paper machine with yankee dryer.
It is found as toilet paper, napkin, kitchen towel, facial paper, paper handkerchief, household paper towel or in sanitary napkin, hygiene products and diapers.
Dust Capturing Concept - Tissue Machine
Dust is generated mainly at the doctor blade (crêping) and the edge trimming (slitting the paper and cutting the edge). On the tensioning roller the unbonded particles of the smoother upper surface are liberated. After the press roller no dust is generated except at the short moment of reel change (paper is cut – teared off).
Dust capturing concept Converting line
During operation at the unwinding belts and at each paper turning point dust is generated. Further, a large amount of dust is produced at and around the slitting position.
Luwa's Complete Dust Handling Solution
Circulaire
Benefits:
- Removes dust from the truss automatically
- Lesser maintenance and cleaning
- No risk of dust lump falling on open paper sheet (converting line)
- Reduced fire hazard
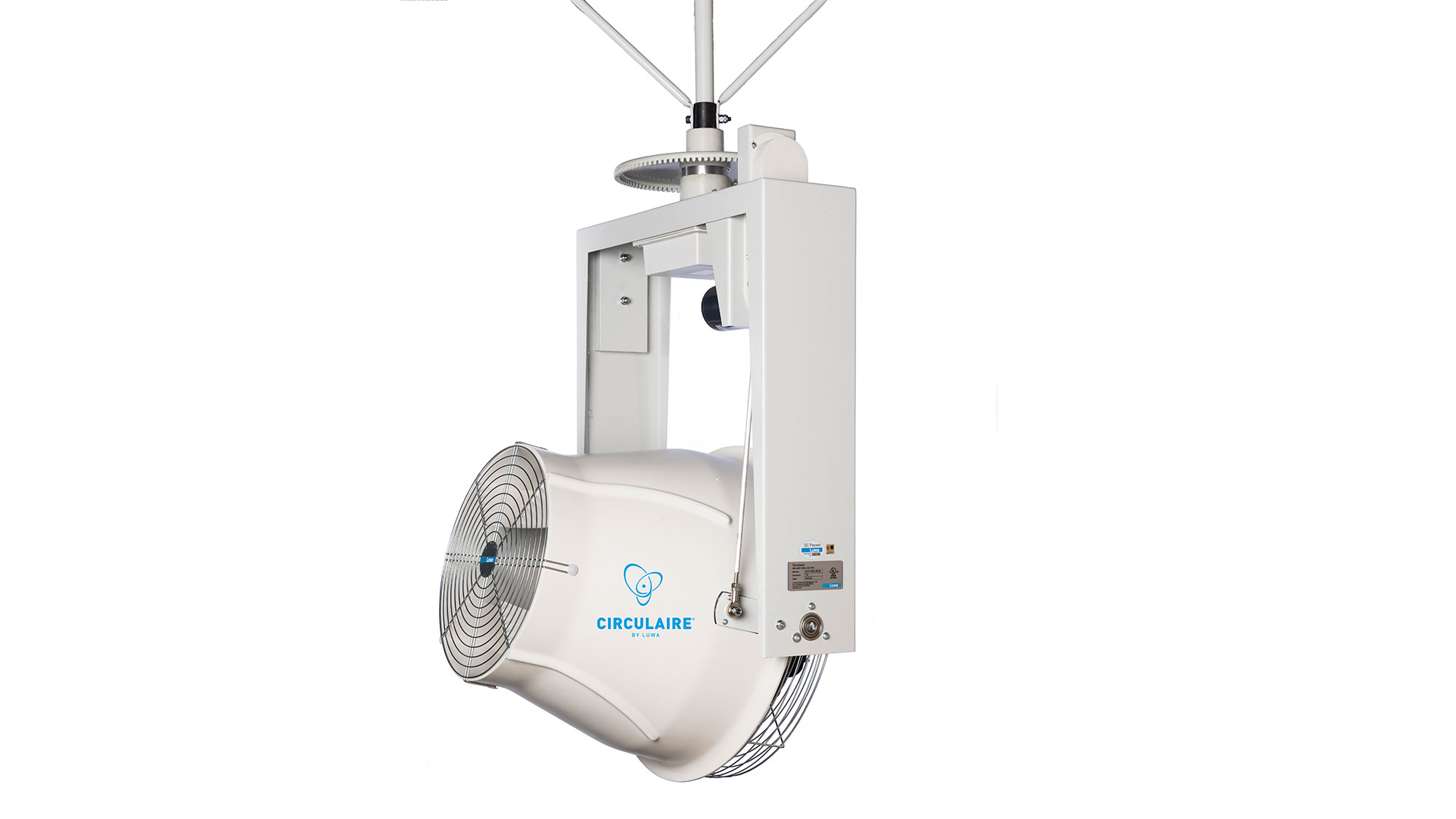
Fresh Air Filter Unit (mosquito preventer)
Benefits:
- Removing mosquitos form entering
- Lesser parent roll rejection
- Keeping department / room in over pressure
- Constant cleaning of fresh air
- Automatic filter recovery
- Improves dust extraction system
- Lesser maintenance and cleaning
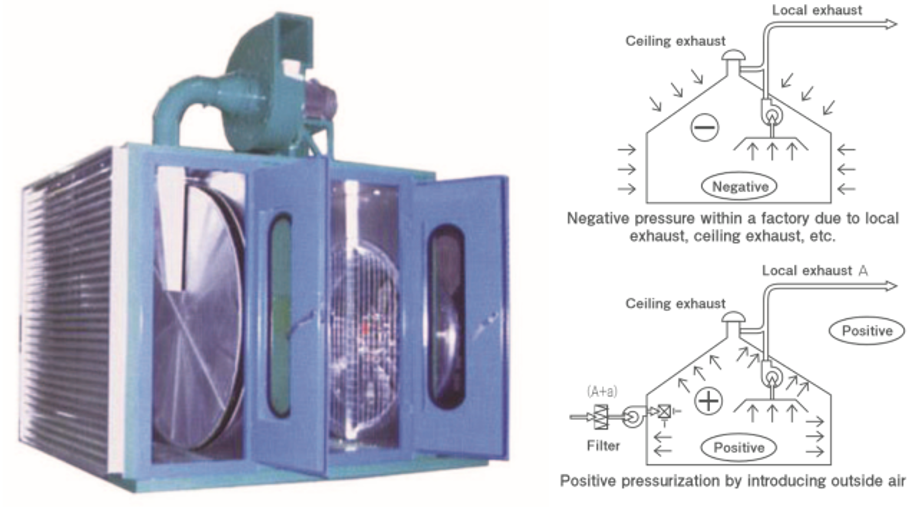
Suction Pipe Design
Luwa uses computational fluid dynamics (CFD) simulation to design appropriate suction pipes to ensure proper capture of the dust right at he source across the tissue web.
Resultant pipe design predicts actual capture velocities at the entrance of the suction pipe and operating pressure drops across pipe components.
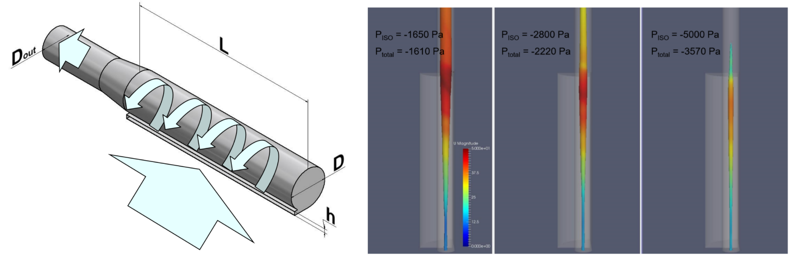
Dust Capturing and Filtration System
Benefits:
- Safer work environment
- Airborne dust regulation conformity and improved air quality for employees
- Improved safety and reduced fire hazard
- Reduced maintenance and manual cleanings
- Improved protection of paper machine and bearings
- Improved product quality
- Improved scanner operation
- Less contamination on rolls
- Higher machine efficiency, fewer paper breaks
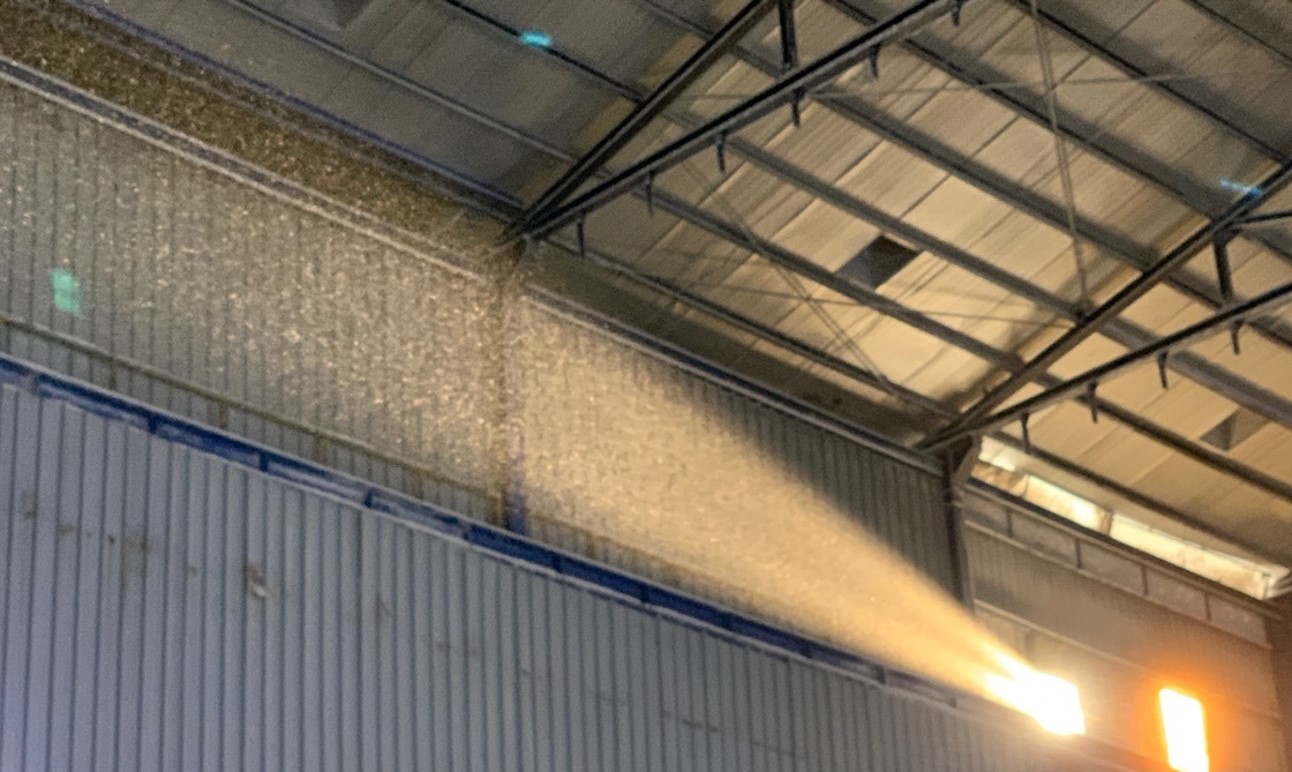
Wet vs. Dry Filter System
- Fire / Explosion proof
- Slurry can be feed back to feed stock
- No labour involvement
- Higher investment cost
- Higher power consumption
- Requires water treatment
- Filtered Air must be exhausted
- Dust collected dry – no waste water
- Lower power consumption
- Lower investment cost for rewinder
- Air can be returned to department
- Limited fire / explosion risk
- Manual dust handling
Nederman MikroPul Venturi Wet Scrubber - Wet Dust Collector
Working principle
- Dust laden gases enters and instantly make contact with the tangentially introduced scrubbing liquid swirling down the venturi’s converging walls
- The gas and liquid streams collide, and the liquid breaks down into droplets which trap dust particles
- Centrifugal action removes the heavy wetted particles from the gas stream
- The dust/liquid mixture is discharged from the separator bottom drain and the cleaned gas leaves through the top of the separator
Wet Scrubber Advantages:
- Paper industry proven design
- Continues dust removal
- Dust slurry returnable to pulp line
- Fire-proof – no need for explosion venting
- Low maintenance cost – no filter media to replace
- Maintenance friendly
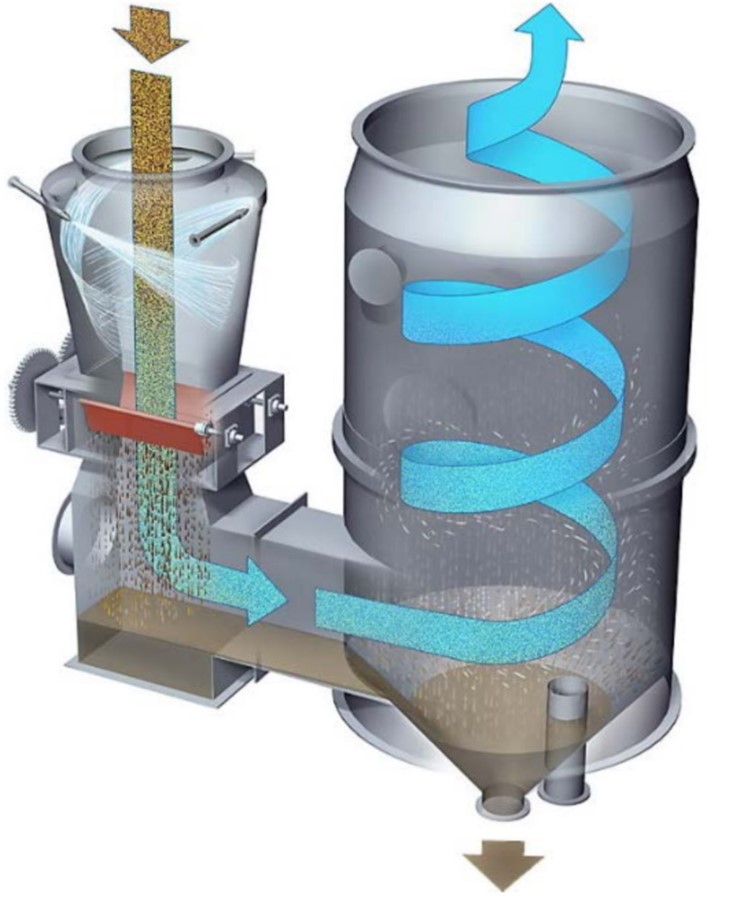
Rotary Air Filter (LDF) - Dry Dust Collector
Working principle
- Dust laden air settles on drum covered with filter media
- The filter drum rotates continuously
- Suction nozzles clean / recover the filter media constantly
- The dust is disposed in a bag
- Ideal for standalone converting lines
Rotary Air Filter Advantages:
- Paper industry proven design
- Continues dust removal
- Dust is collected dry
- Air can be recycled as supply air
- Low maintenance cost
- Low investment cost
- Maintenance friendly
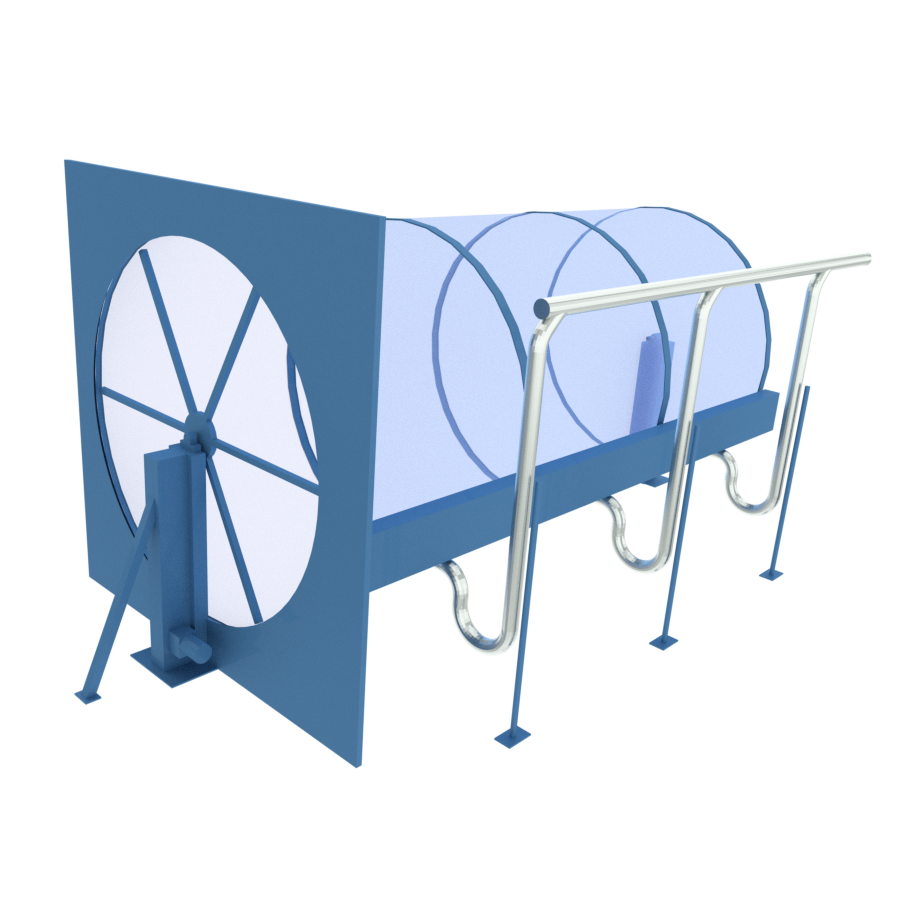
Rotary Pleated Belt Option (RPB) - Dry Dust Collector
Option when space is at a premium and there is a desire to return the air back to the plant.
Working principle
- Dust laden air is collected in high efficiency pleated media
- The pleated media rotates intermittently around two pulleys
- Suction nozzles and pulse pressure clean the filter media at the bottom pulley out of the main airstream to prevent re entrainment
- The dust is disposed into a fine dust filter and either into a bag or to a briquetter
Rotary Pleated Belt Filter Advantages:
- 20 year proven design in operation even including SAP dust with tissue fiber
- Continuous dust removal
- Dust is collected dry
- Air can be returned to the production hall as supply air
- Extremely compact – smallest footprint available per cfm
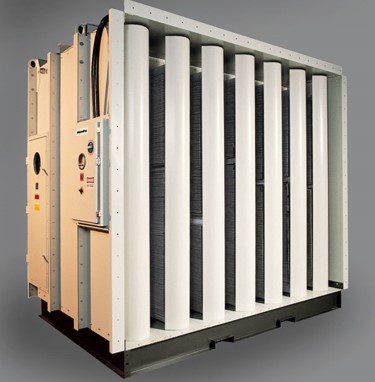
Tissue Trim and waste collection
Preseperator (PSP) can handle large amounts of trim that have been previously chopped into short pieces.
Fiber compactor (FKA) can be used as the secondary capturing device to minimize the volume of waste and dispense into waste containers.
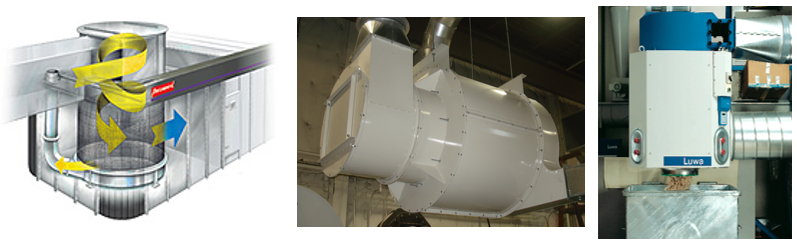
Central Vacuum System
- Less dust on the mill floor
- No compressed air cleaning
- Reduction of fire hazard
- Dust is transported and disposed outside the production area
- Low maintenance cost
- Various suction / cleaning devises and hoses available
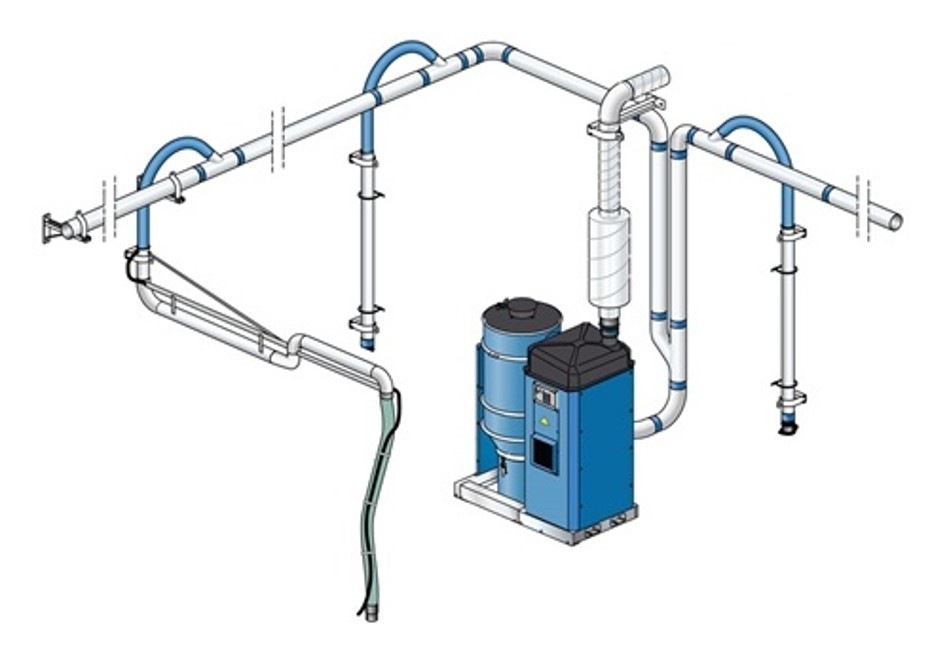