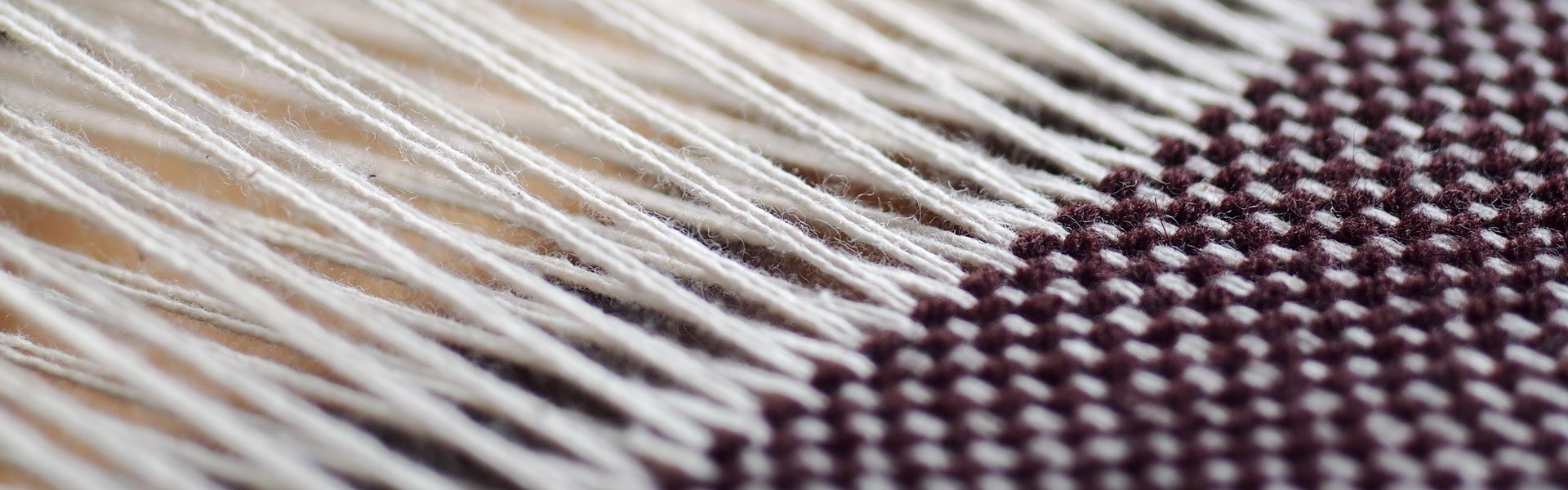
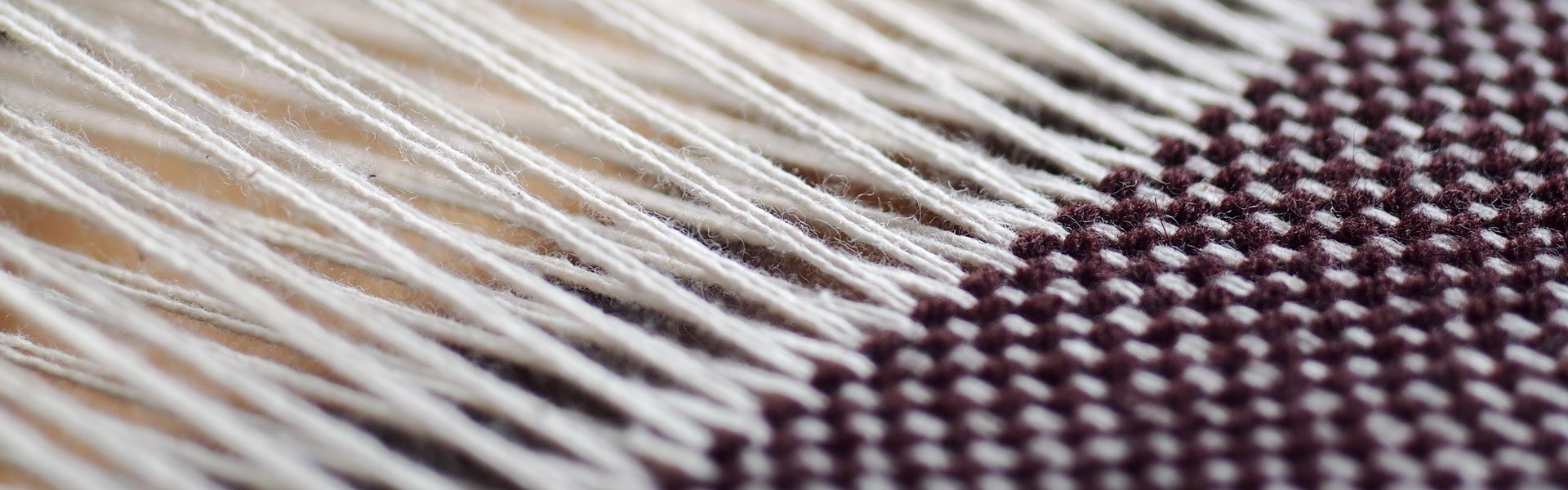
- Home
- Applications
Weaving
Weaving
Weaving of fabric from yarn requires tight environmental control to achieve high quality and high yield. Modern looms operate a very high speeds and generate fluff and fly as well as small amounts of micro dust during production. Moderate amounts of heat are generated by the looms. In addition, the looms require lubrication to work at high speeds, generating small amounts of oil mist. The environment must be controlled in two areas with different targets for each.
The environment at the loom must minimize the buildup of fluff in the loom shed area and supply very high humidity levels to maximize yarn strength and minimize yarn breakage.
Key Factors in Textile & Industrial Air Conditioning
Maintaining the correct humidity level is essential for smooth machine operation. Moisture reduces electrostatic charges, especially on synthetic fibres. But higher humidity increases lapping and reduces the effectiveness of disentangling and alignment. Also, breaking forces and elongation are directly influenced by the ambient humidity in the department. Optimum values vary depending on the use of the raw material and its mixture. A higher relative humidity will result in a lower room temperature during the evaporative cooling mode.
Not all industrial processes are equally sensitive to temperature fluctuations. For example, quenching air processes are highly sensitive and must be controlled within a narrow range. Other processes such as weaving are more accepting of daily temperature fluctuations.
However, all processes prefer a constant temperature, as most fibres and yarns are hydrophilic and the moisture sorption capacity changes with temperature. In addition to reducing count variation, temperature control has a positive effect on:
- reduced fibre fly in the mill,
- fewer electronic failures of the machine control system and
- a better working environment for the employees.
Daily room temperature fluctuations can be minimized by using refrigerant cooling instead of evaporative cooling, especially during the summer months and monsoon rains.
In order to prevent unwanted infiltration of dust from the outside, the mill is kept at constant overpressure. Depending on the outside air contamination, fresh air filters and, depending on the process requirements, supply air filters are required. Local regulations may set Permissible Exposure Limits (PEL) to protect textile workers from byssinosis. Sufficient air changes throughout the mill are required to dilute the dust levels and keep the departments clean and free of fly liberated from the machines.
Fibre Recovery and Disposal - Most spinning preparation machines have integrated suction points that can be incorporated into a fibre deposit system. The fibre separation and dust filtration plant must be designed in such a way that it can handle the required air volume and also the amount of waste fibre.
Depending on the raw fibres used in the plant, several fibre separators can be installed to separate the different materials from each other.
Modern fibre depositing plants are integrated with bailing press systems to automatically store and bale different qualities of waste fibres. This reduces personnel costs and increases the efficiency of the bale press.
The dependency on the fibre depositing system is essential for the operation of the mill. A standstill of either the fibre depositing plant or the bailing system leads to an immediate shutdown of the entire spinning mill.
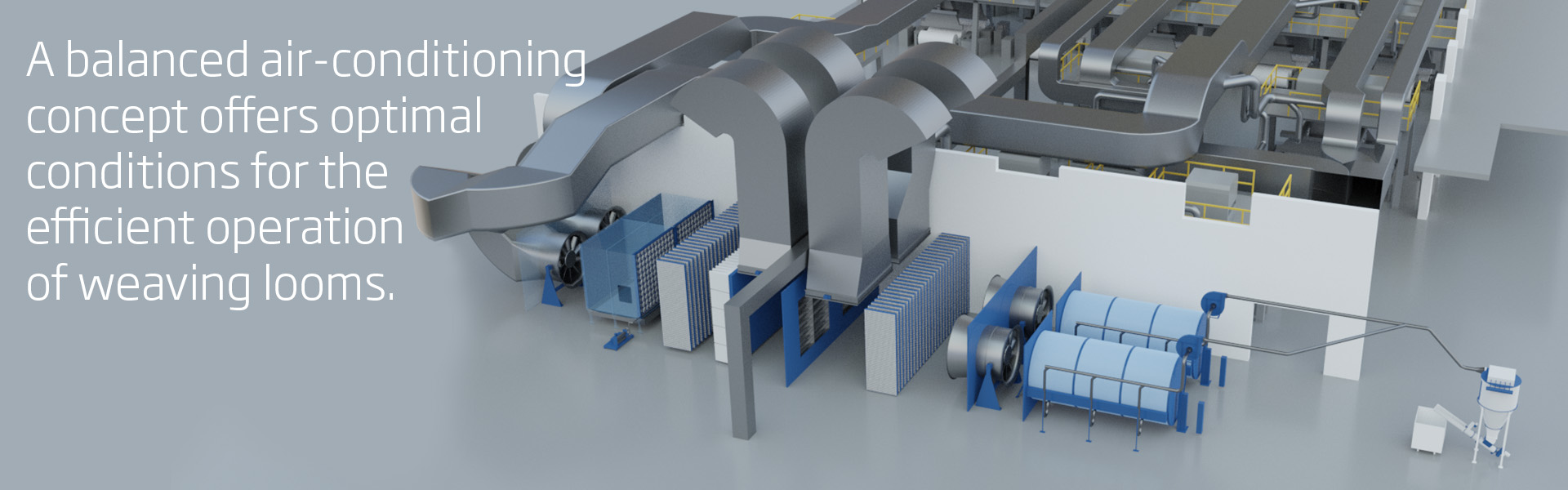
Creating the right conditions for optimal loom efficiency
The Loomsphere System unites all requirements
Profit of a weaving mill is driven by weaving machine efficiency.
Weaving machine efficiency is mainly determined by the downtime in the weaving process due to yarn breaks.
The relative humidity of the environment is an important factor in reducing yarn breaks in natural fibres. There is a direct correlation between the yarn parameters, yarn strength and elongation, and the relative ambient humidity in the production room.
Besides conditioning the yarn with air of high relative humidity, keeping the entire weaving area clean is another prerequisite for an efficient weaving process.
- Laminar airflow - clean air is supplied directly into the weaving zone
- Direct conditioning
- High number of air changes only where it is effective
- Low energy consumption
Functionality
The concept is to ensure high air exchange and humidity precisely where it is needed, rather than throughout the production area. The LoomSphere system is a very targeted air conditioning system.
The LoomSphere diffuser is installed approx. 800 mm above the weaving loom, as required for the harness and beam change.
This arrangement is a result of the high air changes of 80 to 150 per hour required in the weaving area to extract the dust generated in this area. The particularly wide air diffuser with integrated filter creates a laminar air flow that enters the weaving zone without mixing with the dry and dusty ambient air. This laminar airflow concept allows a high humidity of more than 80% at the critical points of the weaving loom.

Conventional system
The entire production room is conditioned to 80% relative humidity. Large supply air volumes are required. The localised heat loads of the looms reduce the relative humidity in the weaving zone to below 70%.
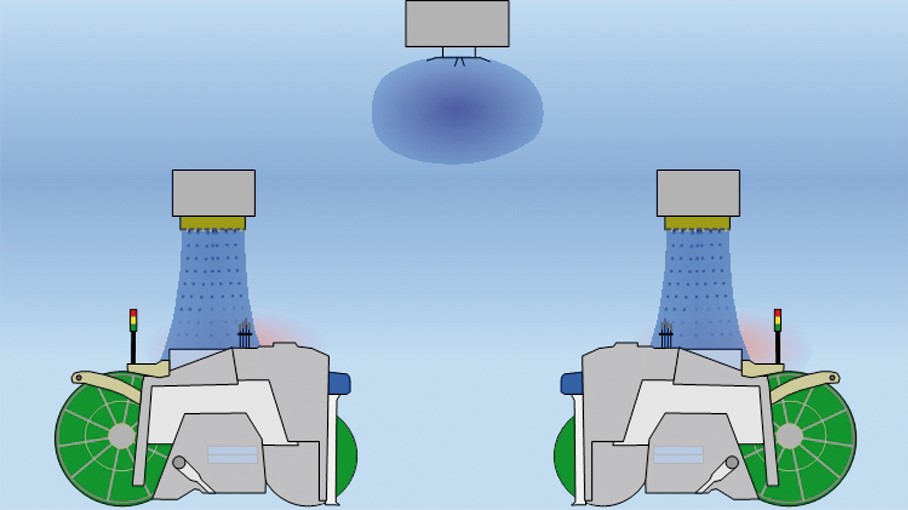
Luwa LoomSphere System
The laminar air supply directly to the loom achieves greater than 80% relative humidity in the weaving zone. The heat load of the weaving loom affects only the ambient room air resulting in a relative humidity in the production room of 65%.
Conventional System | LoomSphere System | |
---|---|---|
Relative humidity room | 80 % rh | 65 % rh |
Relative humidity at warp | < 70 % rh | > 80 % rh |
Air volume of humidification plant | 100 % | 60 % |
Air change room | 45 . . . 60 per h | 30 . . . 35 per h |
Air change at warp level | 45 . . . 60 per h | 80 . . . 150 per h |
Power consumption | 100 % | 60 % |
Process Air Engineering in Weaving Preparation
Importance of Air Engineering
Increased room humidity helps to reduce fibre fly when unwinding the cones and when changing the direction of the yarn on the warping machine. To a lesser extent, this also applies to ball warping and long chain beaming.
High-speed warping machines create a draft of air from the creel to the warping machine. Skillfully placed return air slots in combination with a warper hood reduce fibre fly in the section.
Economy
- Air Flow from 20,000m3/h to 600,000m3/h per AHU
- Variable Air Flow control
Flexibility
- Designs for Indoor and Outdoor installation
- AIr handling unit in modular design
- Components according to process requirement
Luwa Process Support
- Humidity
- Fibre Fly
Main System Components
- Axial Flow Fans
- Air Washer
- Rotary Air Filter
- Air Control Dampers
Textile Air Engineering in Weaving Rapier / Airjet / Waterjet
Importance of Air Engineering
Increased yarn strength improves weaving efficiency. This is achieved when weaving cotton with a high humidity of up to 80% relative humidity. Other fibres, such as viscose, require lower humidity or, like polyester fabrics, moisture to reduce static charge.
High air exchange over the weaving machine is desirable to reduce fly release in the department. Temperature control is used to protect the machines and electronics.
Economy
- Loomsphere System for Energy saving and increased air change across Loom
- Air Flow from 20,000m3/h to 600,000m3/h per AHU
- Variable Air Flow control
Flexibility
- Designs for Indoor and Outdoor installation
- AIr handling unit in modular design
- Components according to process requirement
Luwa Process Support
- Yarn strength
- Humidity
- Temperature
- Loomsphere
Main System Components
- Axial Flow Fans
- Air Washer
- Rotary Air Filter
- Air Control Dampers